Optimale Anlagenkonzepte für die Biopharma-Produktion: Vergleich, Bewertung und Innovation in einer einzigartigen Fallstudie
Waren auch Sie schon einmal mit der Aufgabe konfrontiert, das beste Anlagenkonzept für eine Biopharma-Produktionsanlage zu erarbeiten? Mussten Sie ein Anlagendesign in der Planungsphase fachlich bewerten oder möglicherweise die Projektausführung samt Millionen-Budget freigeben?
Dann ist Ihnen bewusst, dass es DAS beste Anlagenkonzept nicht gibt.
Komplexe Investitionsvorhaben im Pharmabereich vereinen eine Vielzahl von Fachdisziplinen, müssen externe und interne regulatorische Vorgaben berücksichtigen und sollen sowohl bei der Projektabwicklung, als auch im Betrieb bei minimalem CO2 Fußabdruck möglichst kosteneffizient sein.
Dennoch lassen sich diese Anforderungen unter eine Hut bringen. Ein GUTES Anlagendesign ist jenes, das alle Aspekte gewichtet berücksichtigt und in einem definierten Zeitrahmen planungssicher abgewickelt werden kann.
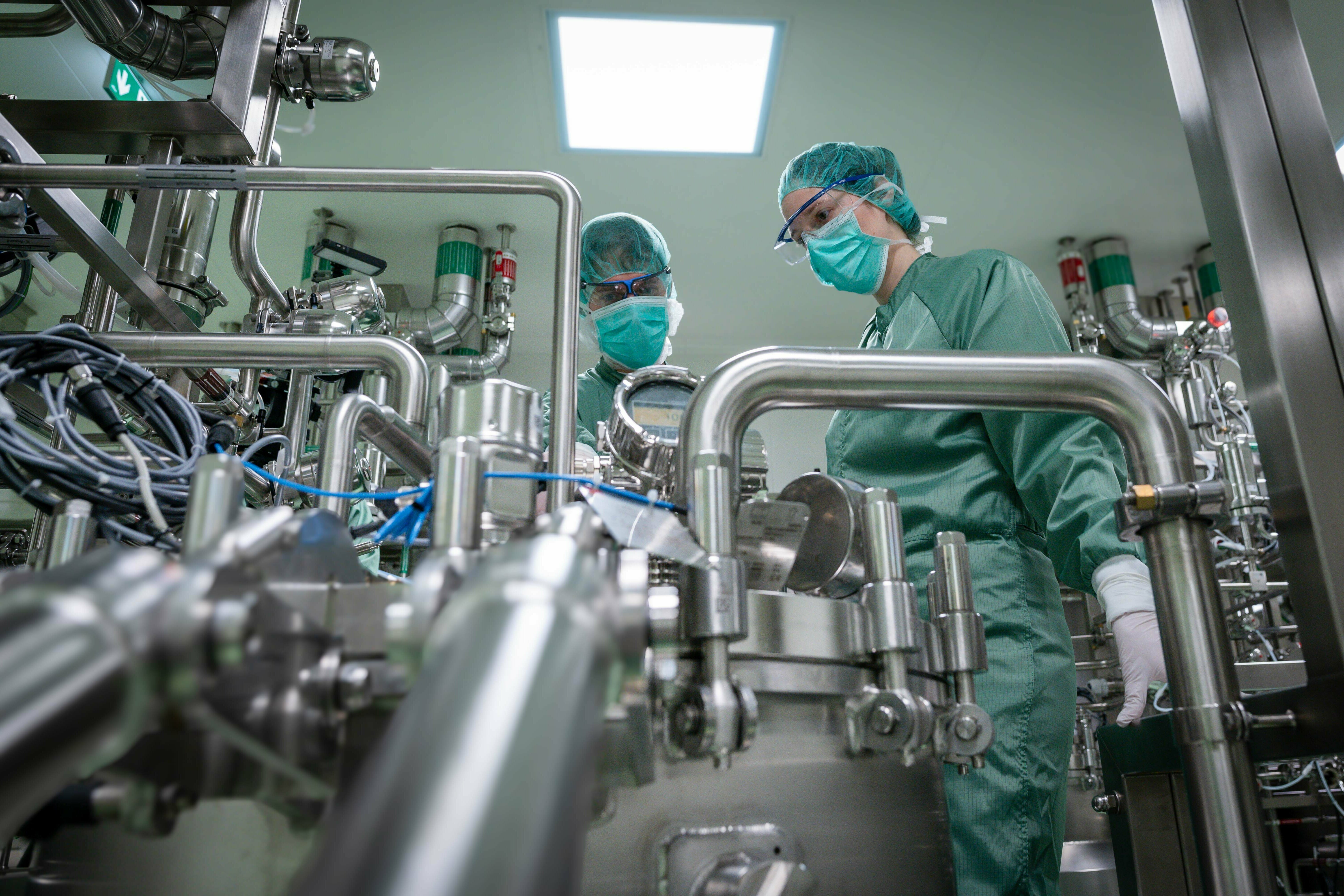
Die VTU Group vereint als EPCMv Generalplaner alle projektrelevanten Fachgewerke, aber auch Expertise im Bereich Manufacturing Science and Technology oder Sustainability unter einem Dach. Dies ergibt einen Pool von 10.000 Erfahrungsjahren in Planung und Expertise - sowohl für die Abwicklung eines Investitionsvorhabens, als auch den Herstellprozess oder Technologietransfer sowie den täglichen Anlagenbetrieb.
In diesem Kontext haben wir eine multidisziplinäre Case-Study für eine Biotech-Großanlage erarbeitet, die fünf verschiedene Designvarianten für den Bereich Puffer eines Downstream-Prozesses gegenüberstellt und als Mini-Serie in 3 Teilen veröffentlicht. Verglichen werden dabei ermittelte Werte für CAPEX, OPEX, sowie der CO2 Fußabdruck.
Es wird eine konventionelle Pufferherstellung und -Lagerung mit großen Edelstahltanks für drei verschiedenen Reinraumausführungen betrachtet, die jeweils aus durchgeführten Projekten abgeleitet sind (weiter unten Fälle A), B) und C)).
Darüber hinaus wird das konventionelle Prozessdesign mit einem Inline-Conditioning Ansatz verglichen. Dabei werden Puffermischungen als Konzentrate angesetzt und im laufenden Downstream-Prozess Inline gemischt und mit WFI verdünnt. Im Unterschied zu Inline-Dilution, wo ein Konzentrat mit WFI verdünnt wird, können dabei bis zu 5 Komponenten oder mehr gemischt werden. Dadurch kann die Anzahl der anzumischenden Konzentrate reduziert werden.
Das Inline Conditioning wird anlagentechnisch einerseits komplett in Edelstahl-Ausführung (Fall D), andererseits aber auch mit dem höchstmöglichen Anteil an Single-Use-Bags abgebildet (Fall E), wobei notwendige Breaktanks, etwa für WFI, in Edelstahl ausgeführt sind.
Was wird dabei konkret verglichen?
Für die herkömmliche Designausführung mit Pufferlagertanks haben wir ein Gesamtvolumen von 250 m³ angesetzt. Dies entspricht einem Gesamt-Bioreaktor-Nettovolumen von 120 m³ und einer angenommenen mittleren Batchzahl von 3,5 pro Woche.
Folgende Fälle werden unterschieden:
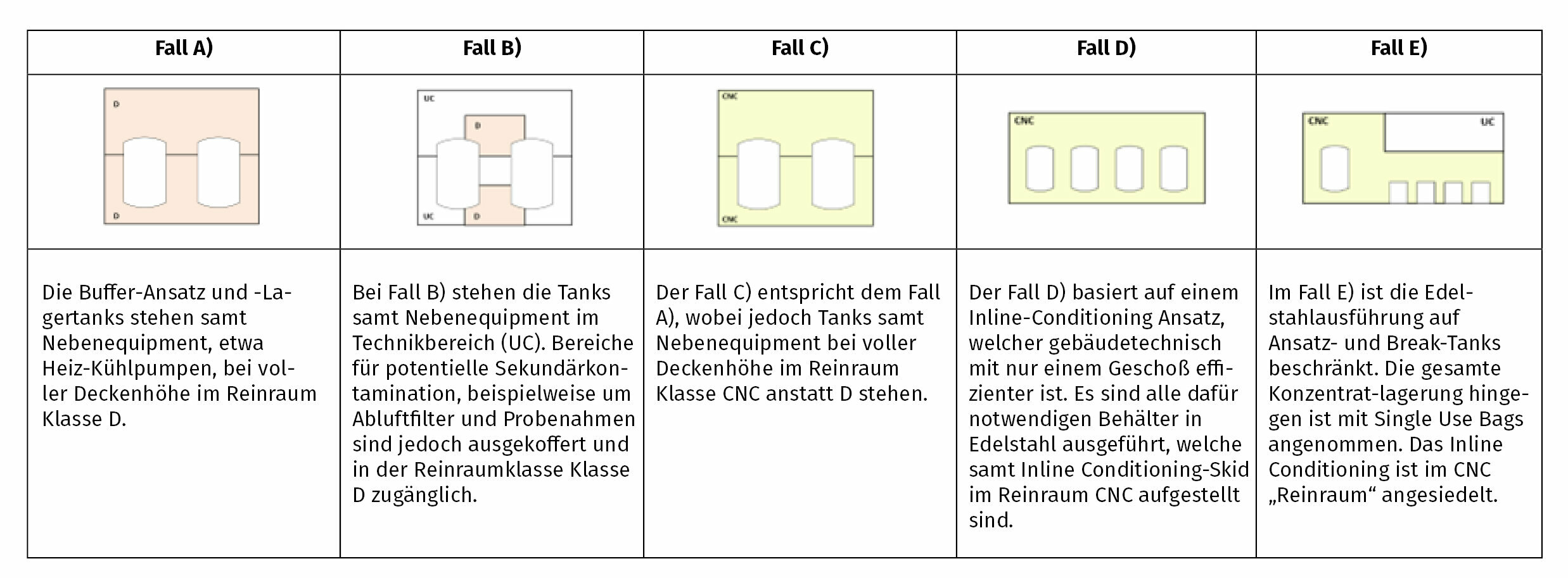
Was sind die Hintergründe für unsere Auswahl?
Der Standard Designansatz ist, die Puffer in Behältern anzumischen und dann in Lagertanks vorzuhalten. Bei Großanlagen ergeben sich dadurch mitunter sehr große Lagertanks mit Volumina von 15 bis 20 m³, die prozessbedingt idealerweise in oberen Stockwerken platziert sind. Dies führt insgesamt zu hohen Kosten für Tanks, Reinräume, Statik und entsprechende Lüftung.
Neuere Designansätze sind Inline-Verdünnung oder Inline Conditioning, die Lagerbehälter minimieren oder sogar darauf verzichten. Bei Inline-Verdünnung wird der Puffer zum Zeitpunkt der Verwendung im Downstream-Prozess aus einer Basischemikalie mit WFI verdünnt, beispielsweise 1molare NaOH aus 25%iger NaOH.
Bei Puffern, die aus gelösten Feststoffen bestehen und zudem aus verschiedenen festen oder flüssigen Komponenten zusammengesetzt sind, ist eine einfach Inline-Verdünnung nicht mehr möglich oder steuerungstechnisch zu aufwändig. Für diesen Fall können jedoch Pufferkonzentrate, sprich Komponentengemische hergestellt werden, die zum Zeitpunkt der Verwendung im Downstream-Prozess „on demand“ gemischt und mit WFI verdünnt werden können.
Bei Inline-Verdünnung und insbesondere -Conditioning ergeben sich Im Vergleich zum Standard-Designansatz, kleinere Behältervolumina und auch geringere Deckenhöhen. Beziehungsweise kann man das Gebäude im Buffer Bereich um ein Geschoß reduzieren und damit auch die damit einhergehenden Kosten samt anteiliger Lüftung.
Allerdings sind für die neuen Designansätze zusätzliches Equipment wie Breaktanks oder eine Vielzahl von kleineren Konzentrat- Lagerbehältern notwendig, konzentrationsbedingt teilweise in Chlorid-beständigen Werkstoffen. Nachdem Instrumentierung und Automatisierung nicht von der Tankgröße abhängen, ist von vornherein nicht klar, ob die neuen Ansätze investitionsseitig auch wirklich kostenminimierend wirken.
Aufgrund der kleineren Lagermengen ist es allerdings möglich, auf Single-Use Systeme zu setzen. Sie reduzieren dann nicht nur Investitionskosten, insbesondere wenn Chlorid-beständige Werkstoffe wie Hastelloy eingesetzt werden müssten, sondern auch den Aufwand für Reinigung und Sanitisierung, erhöhen klarerweise aber die Kosten für Verbrauchsartikel im laufenden Betrieb.
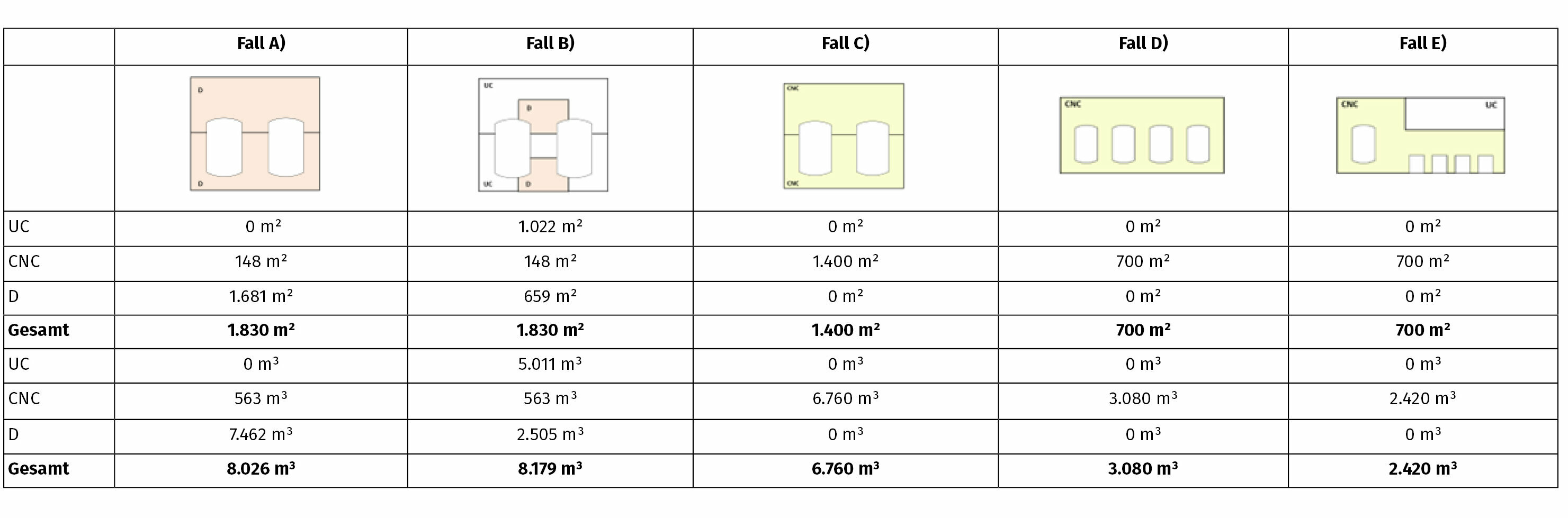
Die Ergebnisse zeigen bereits indirekt das Einsparpotenzial hinsichtlich Investitionen. Der auffallend große Flächenunterschied zwischen Fall A) und C) ergibt sich einerseits aus dem notwendigen Zusatzaufwand an Schleusen und Gangflächen zur Erschließung der Reinraumklasse D über CNC. Zum anderen beinhaltet der Fall A) eine rigorose Trennung von ein- und ausgehenden Materialien, sowie Abfall. Die erschließenden Gangflächen samt Schleusen sind damit im Fall A) in etwa doppelt so groß als für Fall C).
Die unterschiedlichen Geschoßflächen und Raumvolumina haben einen direkten Einfluss auf die Investitionskosten und über die notwendigen Lüftungsanlagen auch die Betriebskosten. Die notwendige Anlagentechnik ist allerdings in den Fällen D) und E) aufwändiger, wodurch sich die Investitionskosten des Equipments hier erhöhen.
Daher stellt sich die Frage wie die verschiedenen Fälle sich in Bezug auf die jeweiligen Kostenfaktoren verhalten.
Im zweiten Teil der Case-Study stellen wir die Investitions- und Betriebskosten (CAPEX/OPEX) gegenüber und analysieren sie.