VTU Engineering is taking over the EPCM for Austria’s largest and most modern plant for the production of vaccines.
The client, MSD Animal Health, will realize two production plants, each with multiple lines operating parallel to one another, at the Krems site by 2021. MSD is a leading global health care company, and a company group of the global US pharmaceutical group Merck & Co. Inc. The group employs around 69,000 employees around the world and, with a sales revenue of just under $40 billion, is one of the largest pharmaceutical companies in the world. Their portfolio comprises medication, vaccines, and biological therapeutics, as well as animal health products. MSD Animal Health is expanding production in Austria and, in doing so, has taken over the former Baxter site in Krems an der Donau. A plant for the production of animal vaccines is planned here. In the coming four to five years, MSD will invest around 220 million dollars (185 million Euros) in the development of the site, and will create up to 400 new jobs upon its completion.
Successful concept design led to general planning contract
In December 2017, VTU Engineering was commissioned with the general planning (EPCM) for MSD Animal Health’s grand project. As early as Fall 2017, VTU had already developed a draft concept in the framework of a feasibility study, and carried out the conceptual design. After the team had proved itself in this phase of the project, the EPCM assignment subsequently took place. As general planner, VTU assumes responsibility for the planning and realization of the entire production plant over the coming years and, parallel to this, also for the construction of the clean room, the quality control laboratory, the capacity expansions for the supply media, as well as for the construction of additional raw material and product storages.
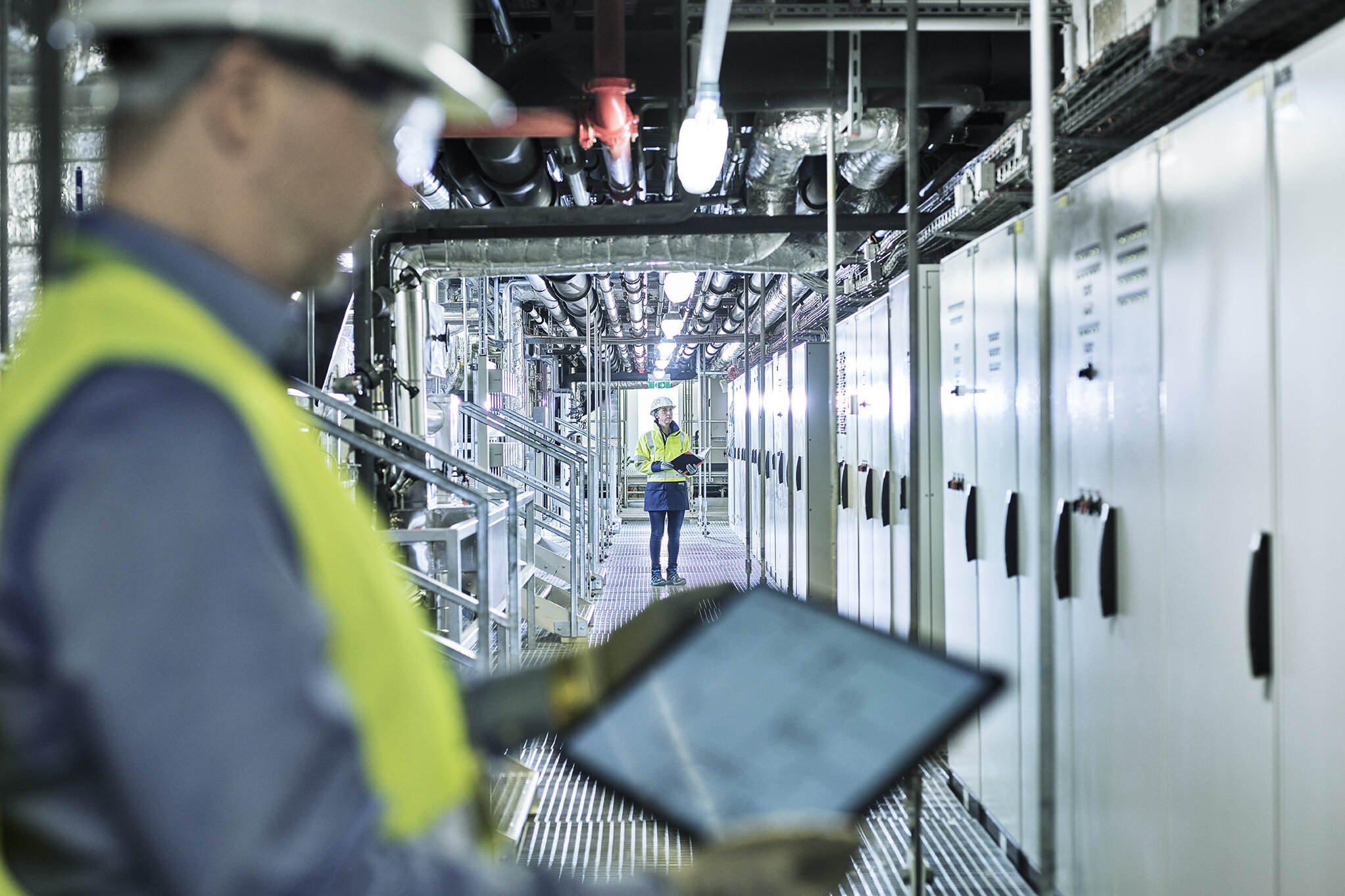
VTU Engineering covers all basic areas for this project in-house, bringing in reinforcement for building, building services, and 3D planning in the form of specialist companies as sub-contractors. The process expertise comes from MSD – the products are already being produced at other sites. In cooperation with international experts from MSD, this expertise will be realized in a modern and efficient plant. A pilot plant will be constructed in the existing clean room area for the optimal transfer of products.
Biotechnological production in accordance with GMP and Sterile Filling
After it is put into operation, the production plant in Krems will be the largest and most modern plant for the production of vaccines which currently exists in Austria. Two production plants with multiple lines operating parallel to one another will be realized by the year 2021, in which antigens, the active ingredients (APIs) of vaccines, will be produced through biotechnological means in accordance with GMP guidelines: one multi-product plant on a bacterial basis, as well as a further plant for the production of antigens with viruses. For the most part, these processes take place under clean room conditions. 30-50 different antigens should be produced in the two plants. With this, quick product changes are a fundamental requirement, and represent a great challenge when it comes to planning the plants.
In addition to the two production lines, a blending and filling plant will also be planned and constructed, where the antigens produced will partly be blended into polyvalent vaccines and filled under sterile conditions. In the course of this project, a third production line with demands on containment as per Biosafety level 3 is also to be planned and taken into consideration, even when its realization is currently still outstanding. An individual production area with Biosafety level 3 (BSL3) must also be constructed for the production of this vaccine, which demands the highest safety precautions and is strongly legally regulated. VTU Engineering is equally responsible for the realization of this production as well as for structural compliance with the strict requirements. Even in a laboratory, BSL3 represents a great challenge. Its implementation in a production plant with permanent operation demands not only biotechnological expertise, but also much experience in engineering, as well as innovative approaches.
Delayed Planning and Start-Up
The planning and construction of the production lines takes place in a time-delayed manner within the so-called workstream. The planning for the plant on a bacterial basis began in December 2017, and the planning for the plant for production with viruses in April 2018. The first plant should already be put into operation by the beginning of 2020 – in spite of partially-existing buildings, this schedule is very tight for a project of this scale. At VTU Engineering, large projects are able to be carried out successfully under time pressure due to well-trained and experienced project managers, due to effective and efficient project development processes, as well as due to the support of software-aided systems which work together optimally.
Decades of experience in international pharmaceutical and biotechnological projects, expert knowledge, and an efficient and effective project management make VTU Engineering a reliable partner for a globally-positioned customer such as MSD when it comes to projects on this scale. Process and production expertise from sites in Great Britain, Germany, Brazil, the USA, and the Netherlands must be combined to create an optimal, comprehensive solution. MSD’s high criteria for security and quality, as well as global GMP regulations, will also be realized as part of the plant’s design and development. In doing so, the production site in Krems will become a model global company for efficiency and product and operating safety.