Conclusion
In Part 1 and Part 2 of this case study, five possible design variants for the buffer preparation of a biotech plant were presented, including the investment and operating costs as well as CO2 offsetting.
In this third and final part, we want to derive the relevance of the data for decision-makers and project managers. The diagram below summarises the key data for the five variants. What conclusions can be drawn from this for future projects in terms of cost efficiency?
Reduction of cleanroom class and room volume reduces costs and CO2
This may be in contradiction to official regulations, however, particularly in terms of factors such as contamination control, operational requirements such as guidelines concerning cleanroom classification and material flow concepts, as well as the specific requirements of the products to be manufactured and/or the manufacturing processes that are planned to be carried out at the plant. The comparison shows that it is certainly worthwhile to question how the external requirements may be met and to consider the different factors from every perspective (planning and/or CAPEX costs, operational management from the perspective of OPEX costs, but also the requirements of the manufacturing process, regulatory and/or contamination control / patient safety).
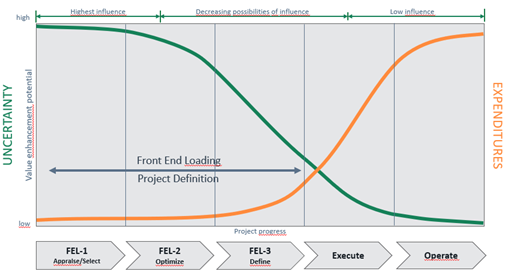
From a project management perspective, these requirements must be discussed in the feasibility study and defined in the concept design phase at the latest, as they have a significant influence on the layout, design and costs. This not only entails considering the requirements relating to the general process operations, but also considering questions regarding:
- Technology transfer
- Cleaning validation
- Process validation
In a feasibility study (FEL0), and sometimes in the concept design (FEL1), the relevant staff units for operations, technology transfer or compliance have typically not yet been integrated into the project. If the costs and CO2 emissions are to be reduced, however, this is essential, and requires planning time. A subsequent assessment can lead to project delays and, depending on the layout adjustments, may require a reassessment of the costs.
Inline dilution, inline conditioning or conventional buffer management?
There is a lot to be said for inline conditioning/dilution – but there are also unanswered questions. Technically, the procedures are documented with sufficient references. Despite this, however, they have to be adapted to the required compositions of the buffers used. This information is not always generally available; for example, the maximum possible concentrations for buffers with complex compositions are relevant, e.g., in terms of the risk of precipitation. Furthermore, questions regarding process validation/mixing studies must be answered or the degrees of freedom for previously validated processes must be considered.
In the case of large-scale plants, it therefore makes sense to answer these questions early on, unless they have already been considered during the process development. The relevant staff units should therefore be included in the initial project phases if an investment project is to be completed within the standard time frame and at reasonable cost.
In the basic design phase, many documents are created that build on each other. Conceptual adjustments during this phase lead to additional costs and often result in project delays.
Are large-scale CO2 neutral plants possible today?
The essential components of the physical plant cannot (yet) be implemented on a CO2 neutral basis. This is due, in particular, to the fact that steel, metals, and concrete are not yet available from decarbonised production sources.
In terms of buildings, the share of such materials can be minimised to a certain extent through the selection of the building components. In terms of the actual process equipment and pipelines, there are currently no real alternatives, however.
Due to the longevity of the structures, the focus of the building should be on usability and adaptability for future generations of plants. As shown, CO2 Emissions from the building structure account for less than 10% over its life cycle, which is why the utilisation should be the focus from the project perspective.
Despite this, however, structures also influence the ongoing rates of energy consumption. With an appropriate orientation and facade design, the future energy consumption can be minimised. VTU offers state-of-the-art optimisation tools for industrial buildings, such as the orientation and size of the window areas, or the integration of photovoltaic modules. The following illustration summarises this:
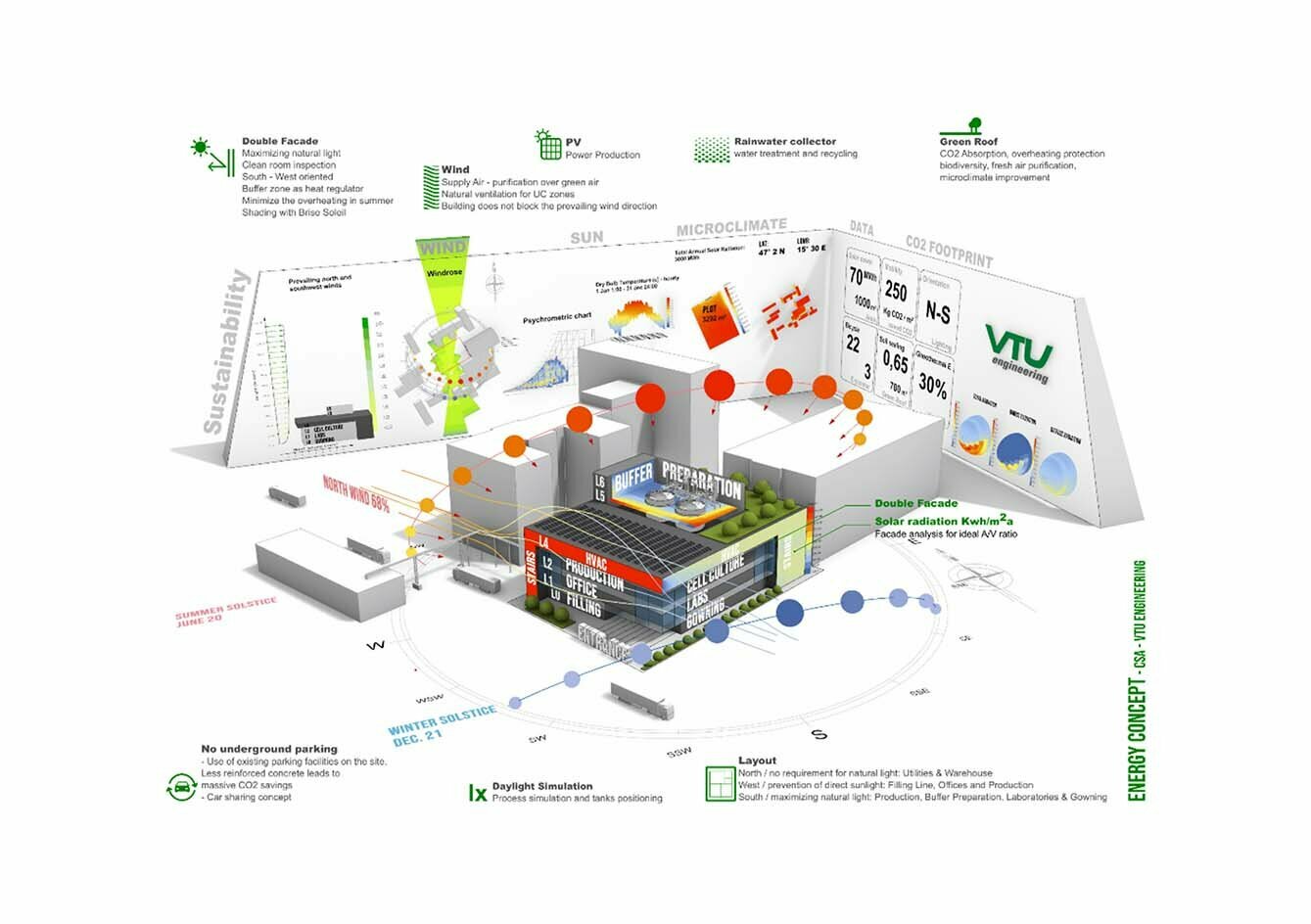
As shown, the lion's share of energy is consumed by the ongoing process operations, which cannot be significantly influenced even with the use of energy-optimised components such as electric motors. In the typical batch operations of a biotech plant, the recovery of process energy is virtually impossible. The secondary use of hot or cold air is already standard practice in the area of building services, provided that it is generated continuously.
When it comes to electrical energy, it is relatively easy to switch to CO2 neutral energy sources – aside from the wider energy policy challenges. Solutions are readily available, and potential additional costs relative to the revenues of biotech plants are not a major obstacle. Many large companies in the life sciences sector have already completed this transition or are on their way to doing so.
Steam generation poses a greater challenge when it comes to decarbonisation. Today, the preferred method is steam generation from natural gas. Alternatives, such as combinations of steam generation and biomass power generation or biogas cogeneration, depend on the one hand on the environment (space, logistics) of the project site. On the other hand, they are often only economically viable on a scale which far exceeds even a large-scale biotech project in terms of energy use. The electrical generation of black steam is rarely implemented but technically possible. In the case of pure steam generators, electrical heating is currently only available as a standard solution for very small plants on the market.
Recurring audits on energy reduction are the state of the art in projects, but they usually only make use of a predefined design concept which they optimise without necessarily examining alternatives. Therefore, in terms of the keyword of decarbonisation, the following should be noted: the key decisions are made in the feasibility study and the concept. However, they often depend on higher-level plant structures, such as central energy generation units, and must be integrated into a holistic evaluation and restructuring of the site.
Conclusion:
Methods for increasing the cost efficiency of plants are common practice in CAPEX projects. However, starting with concept design (FEL1) or basic design (FEL2), predefined plant concepts are usually optimised and long-standing implementation standards, such as the classification of cleanrooms, are often applied.
CO2 neutral plants are not yet possible today, nor will they be in the foreseeable future, taking all supply chains into account. However, reduction measures are already possible today, and in terms of the future, it is worthwhile to start the conversion processes now and to take possible reduction measures into consideration looking ahead.
Alternative concepts would offer greater leverage, but can often only be incorporated into projects if they are considered in the FEL0 and FEL1 project phases and if staff units such as Manufacturing Science and Technology are also involved.
VTU offers “Sustainability by Design” as a related service. Appropriate PM tools such as Green Value Engineering provide support in terms of project management. Sustainability | Free Full-Text | The Green Value Engineering Methodology: A Sustainability-Driven Project Management Tool for Capital Projects in Process Industry (mdpi.com)
Simplified life cycle assessment metrics are used in order to quickly and reliably estimate the reduction in environmental impacts in comparison with a baseline scenario. This allows for an evaluation of potential compromises between environmental concerns and economic benefits, and thus enables informed decision-making.
In this case study, we drew on 10,000 years of experience from employees across the whole of the VTU Group. It reflects some aspects of what forms part of VTU’s “daily business”.